Photo: Multiflo® mega barges on site in Brazil
Dewatering is critical to a mine’s operations and more resources are being allocated to its optimisation. Traditionally, there’s been a tendency among some mine and quarry operations to view dewatering as something to be avoided at all costs – until it can’t be. Therefore, cost minimisation has been the primary focus when it comes to implementing a dewatering or fluid management solution. However, with dewatering becoming increasingly necessary, operators are approaching these challenges in more sophisticated and methodical ways.
The trends informing dewatering practices mirror many of those that are observable across all mining processes: a focus on sustainability and the efficient use of energy and other resources; customised, holistic solutions based on each sites unique geological and climatic conditions; and the emergence of new technologies, with a particular focus on real-time monitoring.
Dewatering solutions that are carefully designed and implemented have the potential to reduce energy usage, CO2 emissions and significantly lower OPEX over the life of the mine. The overall efficiency is affected by individual elements, but also by how these elements interact and operate with one another.
The renewed focus on pumping efficiency requires a significant shift in how many operators have previously approached dewatering and fluid management on site. Because most dewatering programs have been designed with the singular focus of lowering groundwater levels as quickly as possible, they often have excess pumping capacity and oversized pipes and pumps operating at only a fraction of their capacity – a process that’s inherently inefficient. This needs to change to accommodate the increased focus on efficient use of energy and water, which is critical to maintaining a social licence to operate.
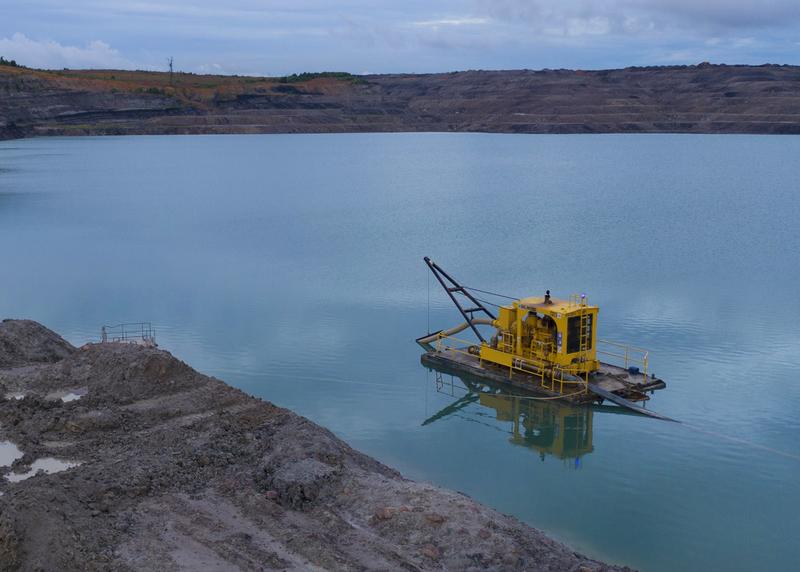
Improving pump efficiency begins with effective monitoring. There have been enormous improvements in electronic control and communication systems in the last few decades. Real time reporting and control of pumping systems can now be an economic reality for almost any mine site. The more visibility you have over your fluid management on site – flow rates, operating pressures, groundwater level, water quality, system relocations, alternate drive solutions, equipment selections to reduce maintenance and repair cycles, etc. – the better placed you will be to install the most appropriate equipment. The industry is moving towards customised solutions and there’s a growing awareness that no two sites are the same, which means a one-size-fits-all approach to dewatering is neither cost effective nor sustainable.
Weir Minerals has a global team of dewatering experts who partner with mine operators to assess their specific requirements and provide integrated solutions. With a long and proud history of innovative engineering, Weir Minerals has a team of process and design engineers armed with the latest technology, specific process knowledge and site experience to optimise your dewatering management processes. We take advantage of our global capabilities and engineering skills to provide our customers with the best solution as quickly as possible.
With an extensive global network and the ability to service on-site or at one of our 130 dedicated service centres, we are always there when you need us - no matter how remote your operation is.